6-minute read - by Brittney Wolff Zatezalo, May 6, 2020
Travel restrictions due to the coronavirus (COVID-19) pandemic mean that some of our customer support engineers can’t visit our chipmaker customers’ sites to help them keep their lithography machines up and running. During a crisis that could have cost ASML millions or even billions, a cross-functional team used gaming-inspired augmented reality to turn a potential problem into a new opportunity to help our customers remotely.
Within a matter of days following the travel ban from Europe to the US, a joint task force of more than 100 ASML experts mobilized from their homes around the world.
Their mission: Make sure that our multi-million-dollar, state-of-the-art chipmaking equipment stays running at customers’ sites in the midst of a global pandemic. The team quickly developed an augmented reality (AR) solution, enabling subject matter experts to ‘enter’ the cleanrooms in customer fabs (factories) to complete service actions and troubleshoot other issues.
“The silos quickly disappeared,” says Peter Peusens, head of Customer Support DUV Operations and project lead of the augmented reality task force. “It was merely a matter of managing the enthusiasm of everyone to walk in the same direction.”
Every 24 hours yielded substantial progress, as sub-teams met daily within Microsoft Teams to discuss accomplishments and new tasks to be tackled within a day. After quick factory testing at ASML Wilton and Veldhoven, the Netherlands, the team successfully utilized AR on a smartphone as well as a Microsoft HoloLens headset to complete a full service action on March 20 at a customer’s site.
Origins in gaming-inspired virtual reality
The immediate solution only took a few weeks to go from inception to application, but this was because a grassroots effort had begun to lay the foundations several years earlier, enabling a quicker response in the face of a crisis.
In 2018, Thomas Weinlandt, a mechanical engineer in Wilton, Connecticut, bought a discounted virtual reality (VR) headset with his own money, recognizing an opportunity to apply his hobby at work. Through a grassroots effort, he quickly embedded the capability throughout various teams and locations at ASML, who use it for reviews early in the design process.
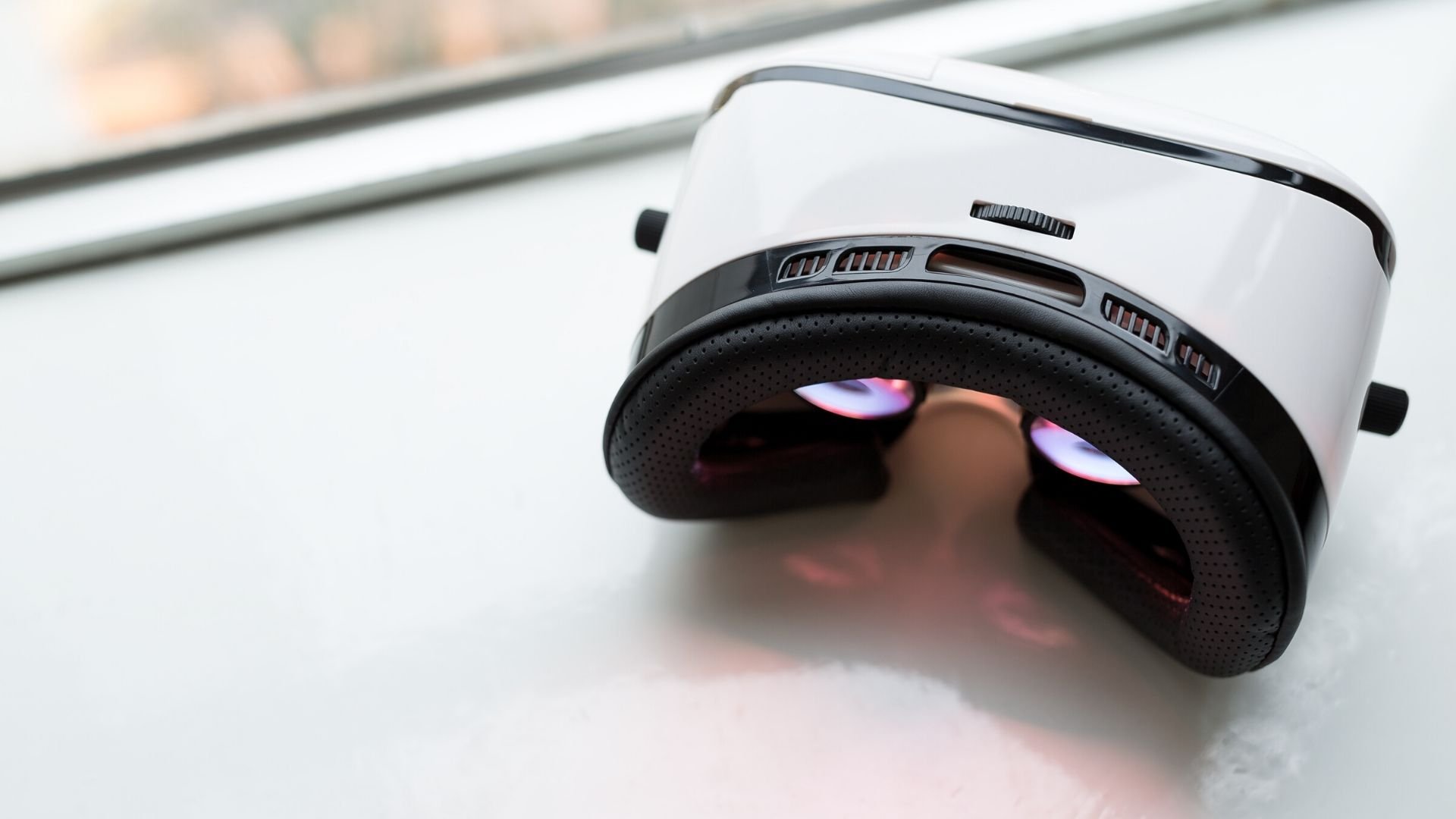
Virtual reality enables engineering teams to catch design flaws earlier and make simple changes, while actively collaborating with manufacturing teams to better address serviceability.
VR isn’t only an enabling technology – it’s an essential communications tool. For a global company where only 10% speak English as a first language, it provides a visual and intuitive way to understand how a designed system will be serviced, accessed and assembled.
In Wilton, it also cut development time of a critical mechatronics sub-system (the reticle stage) from several years to three months, and improved availability by 10%.
Accelerating the roadmap in the face of a crisis
But much like it did everything else, the quickly evolving COVID-19 epidemic changed the game for VR at ASML. Even though virtual reality had previously proven its value for design work, it was much more challenging to apply as a service tool, when two people at different locations need to collaborate on complex assemblies in real time with dynamic information. This scenario became a reality in March 2020, when due to coronavirus-related travel restrictions, ASML could no longer fly out experts to solve on-site customer issues themselves.
The stakes were high. For every minute that a system is ‘down’ at a customer’s site, the customer can potentially lose thousands of dollars. This quickly escalates to millions of dollars if it’s down for a day or more.
ASML needed a solution, and needed it yesterday.
“Everyone understood the dynamics of the situation. These were not normal times – we needed to quickly pivot,” says Keith Braunmueller, group leader at ASML Malta. “What typically takes us weeks to plan, we completed in a matter of days. It’s a true testament to our team and customer’s willingness to quickly discuss concerns, how to mitigate them and develop practical solutions. Plus, it’s not every day we get to work with augmented reality. We were all very interested to see how the technology could help us.”
The first service action using augmented reality
The team successfully completed a service action at a customer’s site using AR on Friday, March 20. “We were able to see it through their eyes,” Keith recalls. “With real-time feedback, we were confident that we were both looking at the same thing and understanding it in the same way. It was a very efficient troubleshooting and communications tool.”
Engineers are transported into a ‘Minority Report’ world, but quickly learn within a few sessions how to merge their physical and augmented reality environments. “If you would have told me a month ago a customer support engineer in the US or Taiwan would complete a service action with a HoloLens, I would have laughed in your face,” says Peter. “But it’s more than a novelty. We’ve now shown its real business value.”
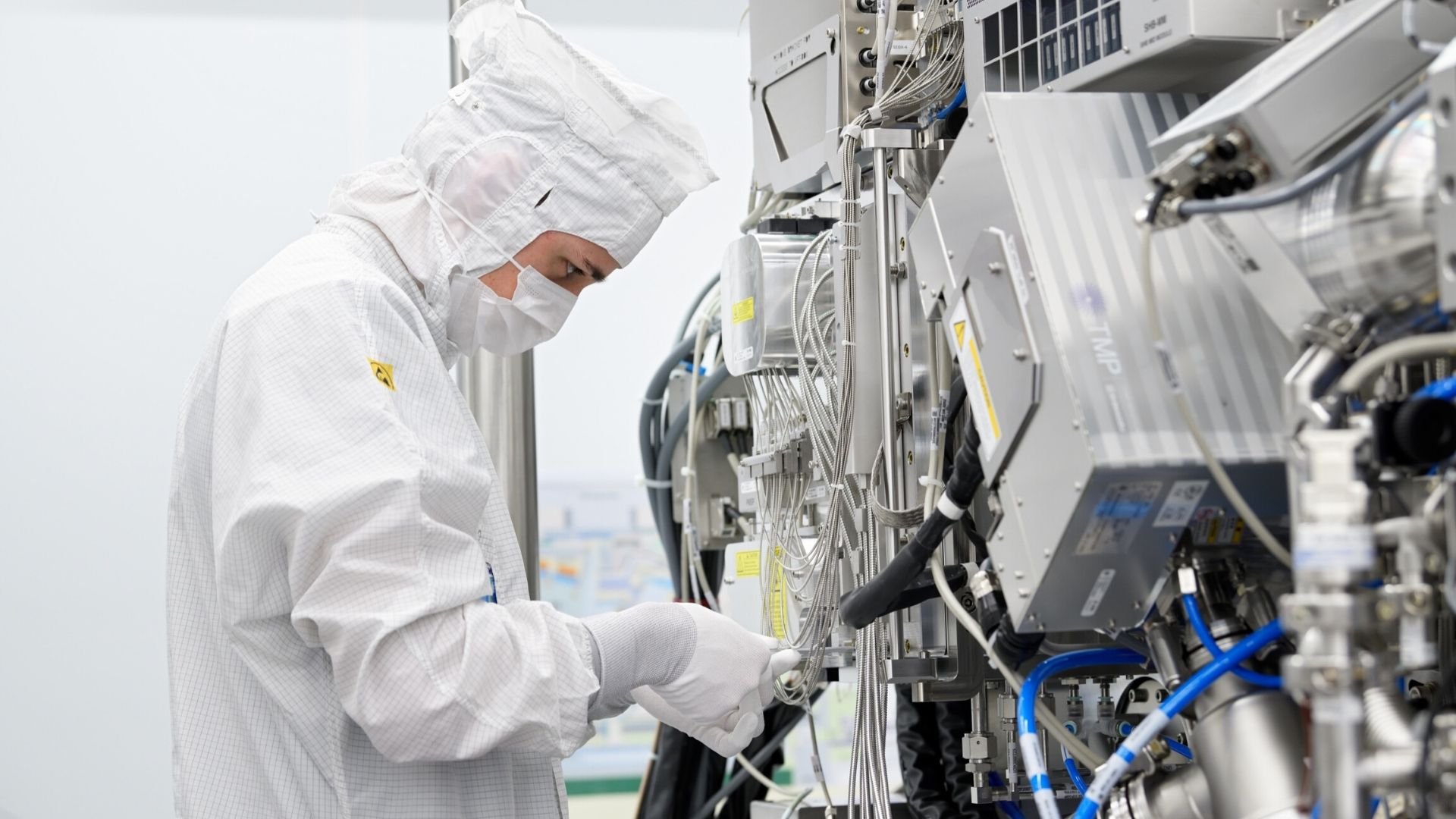
Thomas adds, “With augmented reality, we are able to have our top experts support our machines anywhere in the world with effectively 24/7 uptime. The ability to instantly deploy expertise anywhere in the world is going to be a game changer.”
Augmenting expertise
Virtual reality will never be able to replace true experience or expertise in the field. It could actually help the experts providing it. Here the desire is to keep experts in their wheelhouse, while building a more effective bridge for diverse teams to collaborate and find the best solutions together.
“We normally rely on procedures in the field, but there’s a lot of information from experience that can’t be captured in a procedure,” says Keith. “Augmented reality allows us to talk our on-site customer support engineers through lots of tips and tricks, while doing the action.”
Engineers can be engineers again, instead of administrators, bringing knowledge directly to engineers at the best time and in the best format.
Think of it this way: You can’t put on a HoloLens headset and suddenly become a star NFL player, but you could become a master chess player because this knowledge can be transferred more effectively via real-time coaching.
“Our people can have good hands, but not all the skills needed to complete a specific service action or troubleshoot an issue,” says Jared Fredrick, manager of our DUV Global Customer Support Center for North America. “Alternatively, we have people with expert eyes who are more attuned to see certain things that people in the field might miss, spot dynamic short cuts or quickly determine if something is broken.”
Challenges in virtual reality
Using augmented and virtual reality in customer support at ASML is certainly a game changer, but it comes with challenges. One challenge is the security of intellectual property. If intellectual property didn’t matter, everyone would be using VR tomorrow. But security remains a concern on both sides and an ongoing research and development focus area.
“Shifting to a more agile way of working last year, the IT team truly transformed to be a strong business partner delivering a highly secure solution,” says Vincent Verpoort, value stream manager for Information Services. “We quickly integrated feedback and established simple principles to establish trust and confidence with our customers.”
“Even though we quickly overcame initial roadblocks at a few customer sites, it’s still very taboo to have a camera in the field, let alone a streaming camera,” says Jared.
ASML is taking steps to make sure that security remains a top priority. “We’ve formed a cross-functional team with our customer that includes IT security experts, and our internal project team is mapping out how to use the technology in the future. In the meantime, we’re also improving our IT and infrastructure in order to protect everyone’s IP,” adds Vincent.
A promising road ahead
Although it’s still in the early phases, the cross-functional team is using augmented reality to complete service actions more and more every day. They are proving that despite increasingly difficult access to customer sites, restrictions on physical movement don’t spell the end of timely customer service.
“There is a clear time advantage to using augmented reality for unforeseen escalations, which before would take a minimum of 24 hours to respond,” says Keith. Although he doesn’t see as much value for planned and complex service actions, the team plans to continue to explore the best long-term implementation of this technology for both ASML and our customers.
Jared add, “As we look back at the past few weeks, we are very proud of the tremendous support, care and open communications the teams provided to all involved.”
“While the joint task force tackled 80% of the solution, I’m amazed by the remaining 20% gap that was and continues to be closed by our engineers in the field where it comes down to actually making it work, their expertise and attention to detail is unparalleled,” concludes Vincent.
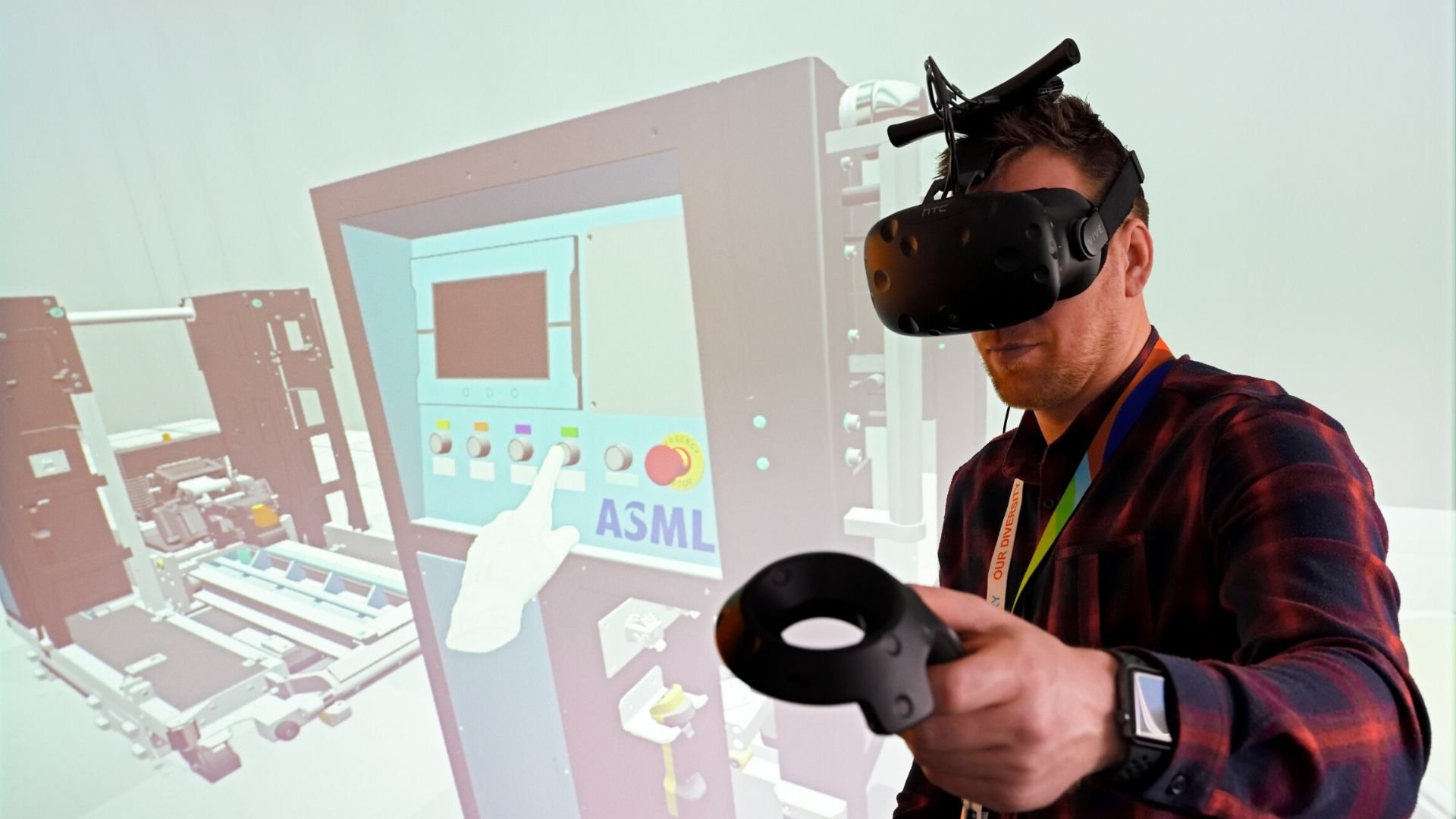