4-minute read - by Christine Middleton, March 15, 2023
ASML has an ambitious target. We’ve committed to reaching a re-use rate of 95% by 2025 for parts returned from machines in the field and from our factories. And we’re well on our way: The re-use rate rose from 85% in 2021 to 87% in 2022. (For more information, download our 2022 Annual Report.)
Our Re-use program makes us better able to ramp up our capacity to cope with strong customer demand. Because we can retrieve parts from inventory or through repair or harvesting, we’ve been able to start building extra modules in our workcenters. That’s helped to speed up the implementation of re-use across our company.
Here are seven important ways we’re tackling the technical and logistical challenges behind increasing re-use.
1. Designing for re-use
An important element of developing a sustainable circular economy is designing for circularity. That means planning for new parts to be repairable and upgradeable.
Two key considerations when designing for circularity are modular design and commonality, both of which are featured in the designs of our lithography systems. Through modular design, we make sure that worn parts and components can be replaced as a single unit. And by ensuring commonality, we enable parts to be used in multiple contexts, both within a machine and across different systems.
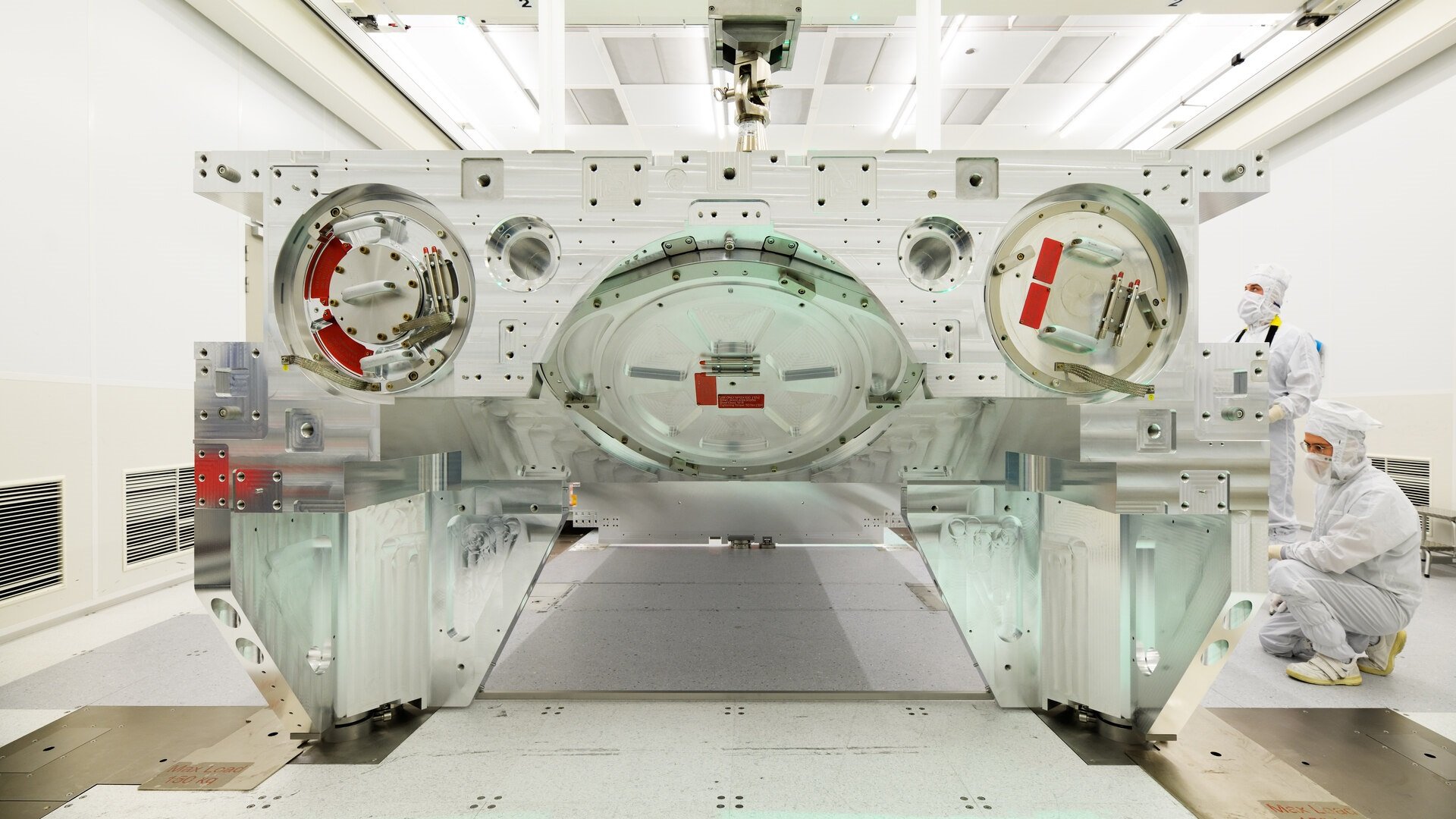
2. Saving transport materials
Re-use isn’t just for the parts in our machines. It can apply to anything that might get thrown away, including the materials – parts, tools and packaging – that we use to keep our products safe during shipping.
Our customers send transport materials back to ASML for the original supplier to bring them back into the supply chain. The materials go through a quality check before being re-used. We’re working to standardize this return process in a network-based way to make the return process easier and more efficient. That standardization can also lower the effective CO2 footprint of re-use by reducing transport.
Our aim is for 80% or more of transport materials from an installation or relocation to be returned and re-used.
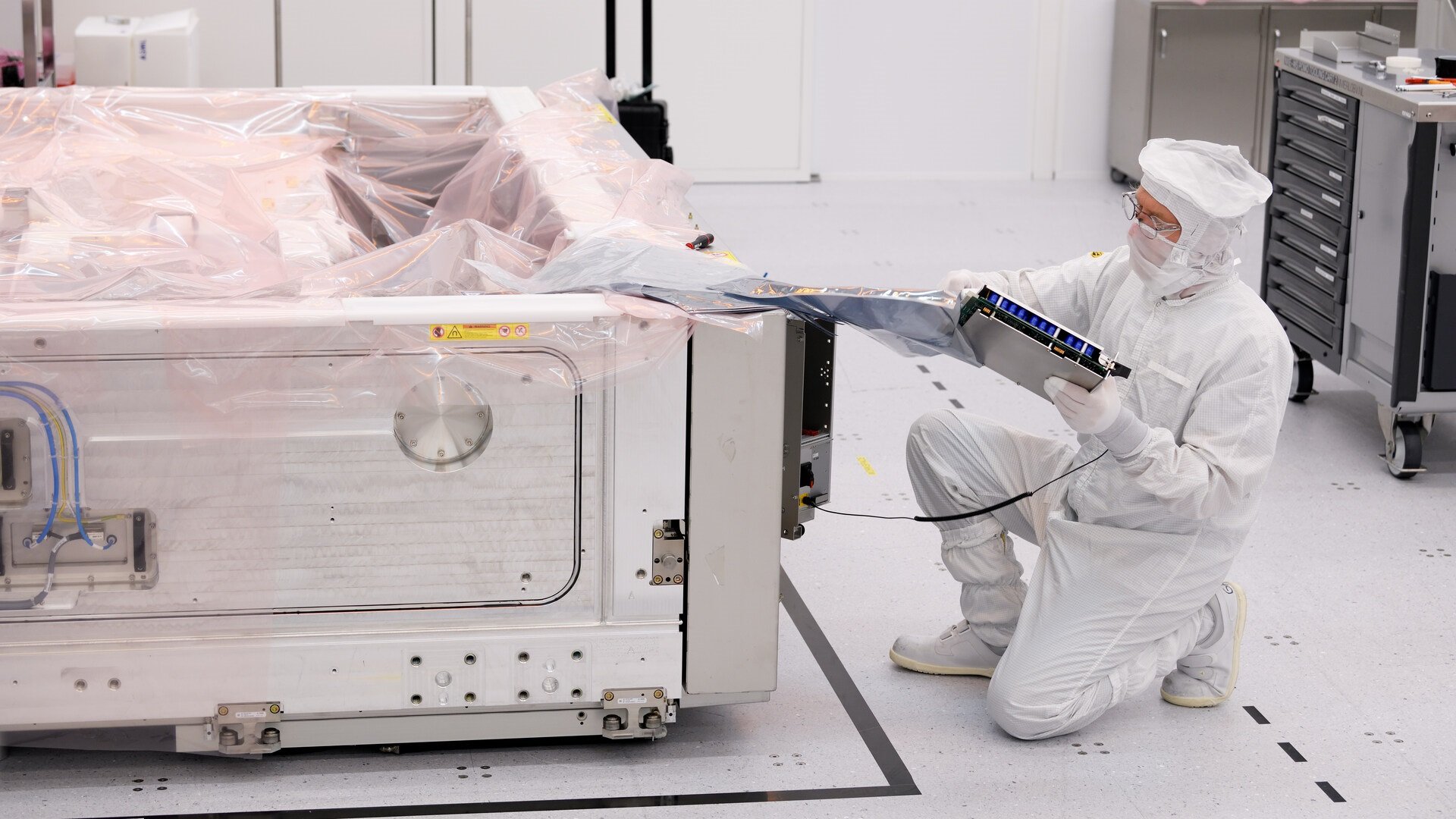
3. Localizing
When a part from a machine at a customer facility needs to be cleaned, refurbished and repaired, it’s expensive and time consuming to send it back to an ASML manufacturing location. That’s why we’ve established local repair centers to handle those tasks. Keeping repair and re-use activities close to the customers reduces service time and improves part availability.
By 2025, we aim for 10% of parts in the field that need service to be repaired locally. And because the parts won’t have to travel as far, the repair will produce fewer greenhouse gas emissions.
Our repair centers create a local ecosystem by partnering with local material suppliers and specialized repair partners. We currently have local repair centers in the Netherlands, the US, Taiwan, South Korea and China, and we plan to eventually have at least one center in every customer region.
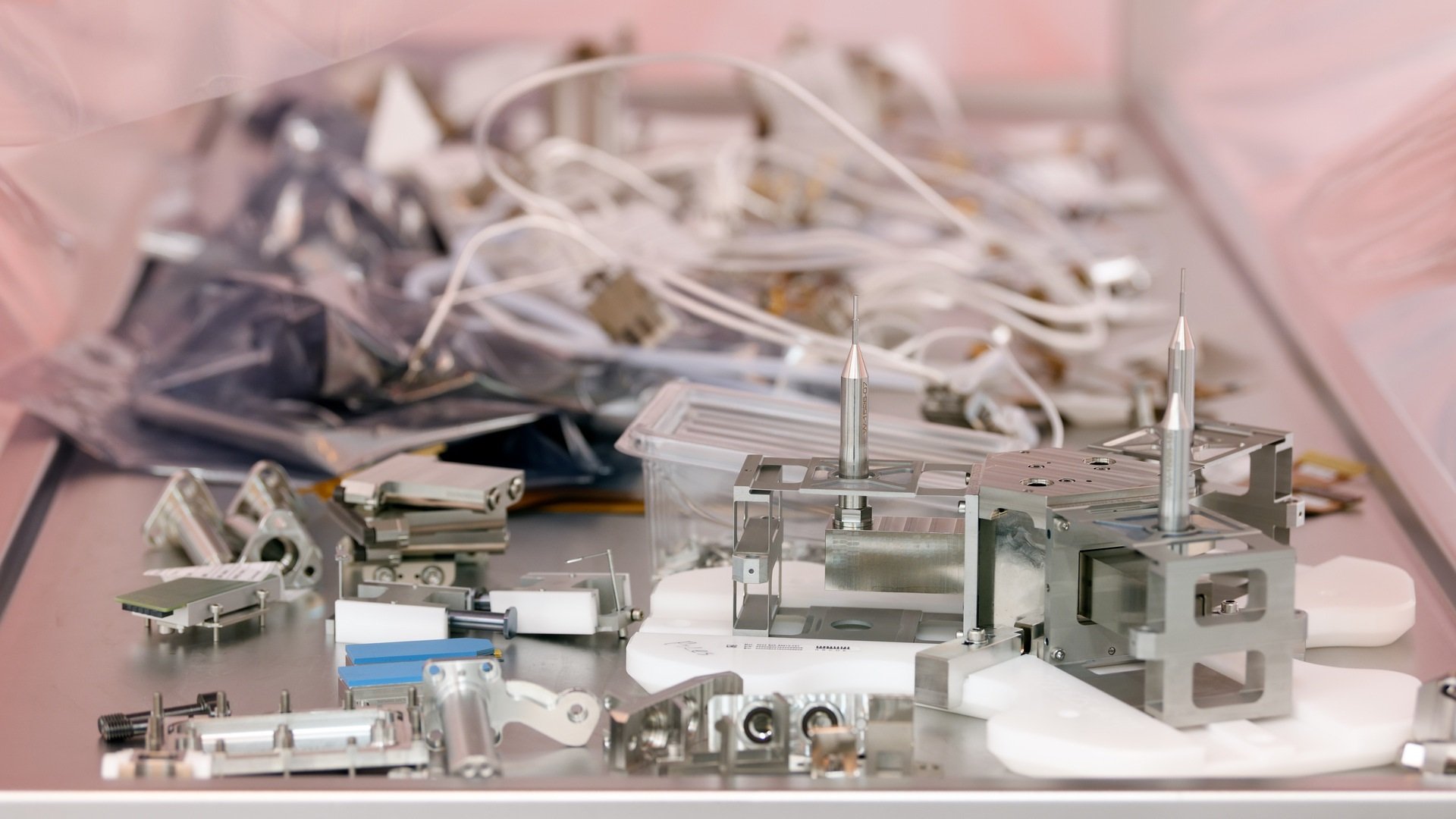
4. Collaborating
Our suppliers are a critical part of our supply chain and production process. So to meet our re-use goals, we need them on board.
ASML recently hosted a four-day workshop with five suppliers who were looking for more ways to incorporate re-use into their work. We plan to expand this successful pilot program to include more of our suppliers.
As part of our Supplier Sustainability Program, we ask suppliers to sign a ‘Letter of Intent’ that includes a commitment to collaborating with ASML and our ecosystem partners on maximizing re-use. In 2022, 59% of our suppliers made that commitment; we hope to reach 80% by 2025.
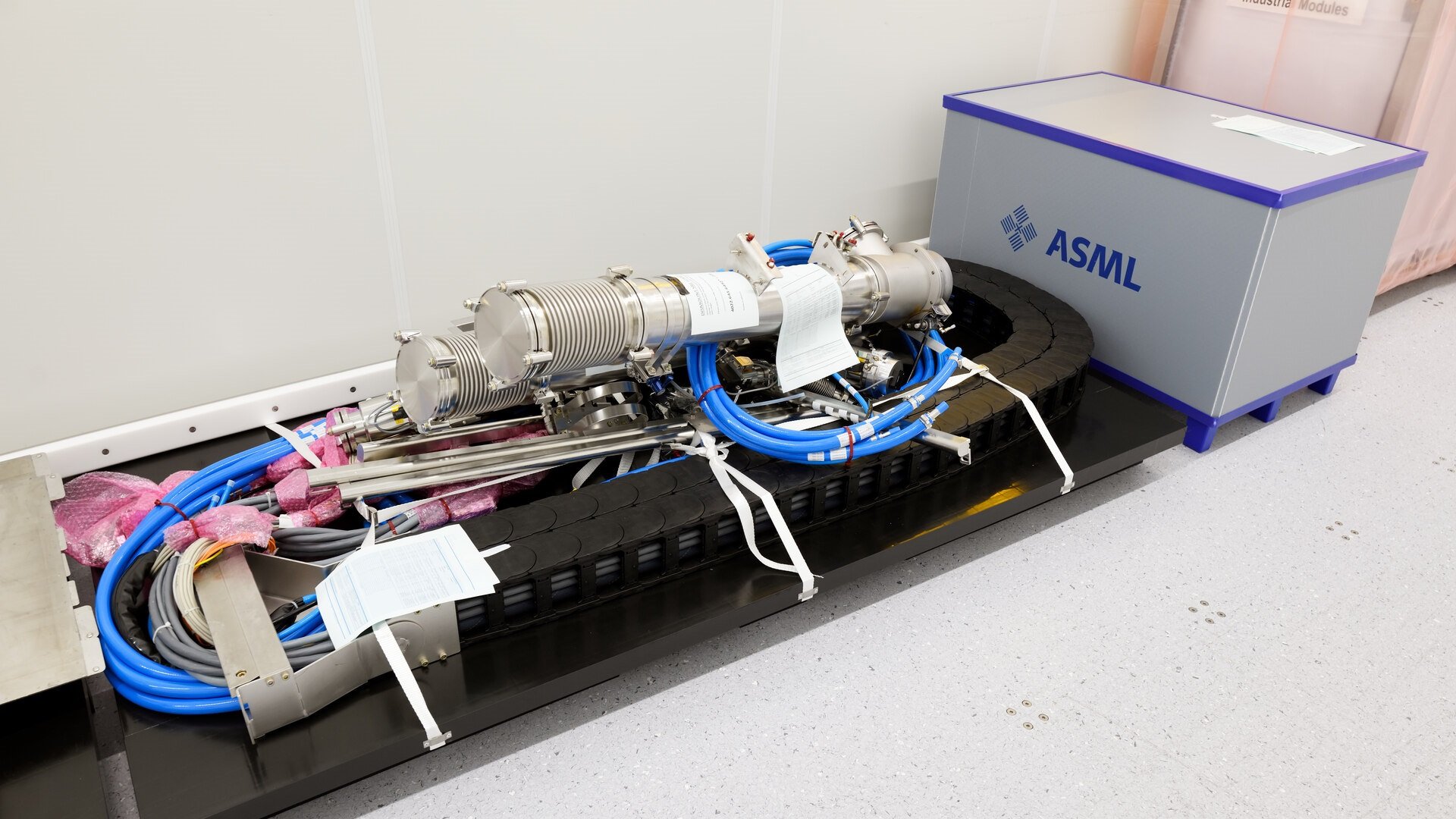
5. Refurbishing parts
How do you ready a part for re-use? Each system component requires its own process for returning it to as-new condition.
One part for which we’ve successfully established a refurbishment process is the external interface module, which regulates gas flows into our deep ultraviolet (DUV) TWINSCAN XT and NXT systems. The module is produced by our supplier Lamers, which is part of Aalberts Advanced Mechatronics in the Netherlands. Together we showed that rebuilt modules could reach as-new quality. Re-using one of those modules saves about 200 kg of waste and between €40k and €50k.
Re-use is also part of our extreme ultraviolet (EUV) systems. For example, we’ve teamed up with our supplier VDL to create a process for retrieving, disassembling and draining the buckets that collect liquid tin from the light source.
6. Standardizing quality
When a part is re-used, our customers expect it to be as good as new. That’s why we require all refurbished parts to meet the same standards as new ones. And we expect our suppliers to meet the same standard.
Re-use also teaches us how to provide even better quality to our customers. When we go through the process of repairing and qualifying parts for re-use, we learn more about how each part works and ages. By implementing those learnings in our designs, we can improve the parts and deliver better system performance and lifetime moving forward.
7. Preparing to grow
A lot of our re-use activities are currently handled by the same workcenters that build new modules. But the number of ASML lithography systems in use continues to grow, so we’re going to need dedicated centers to handle the higher volume of re-use parts. That’s why we’re building dedicated global re-use centers to handle re-use activities for factory materials.
One such repair center is already open in Linkou, Taiwan, and we’ve started building one in Veldhoven, the Netherlands. We’re also establishing centers near our manufacturing sites in Wilton and San Diego, both in the US.
All this re-use will mean less material potentially heading to landfills and incinerators. But it also translates to big savings. In 2022, ASML saved €781 million by re-using service parts, up from €686 million in 2021. So it’s a win–win situation: What’s good for our business is also good for our planet.