What is a light wavelength? Like waves in the sea, light travels as a series of peaks and troughs. The distance between the peaks is called a wavelength. The shorter the wavelength of light, the smaller the microchip features that can be printed in a lithography process.
Throughout ASML’s history, we’ve supported chip manufacturers in making the transition to new lithography wavelengths that make more advanced microchips possible. Each step forward required innovation in how the light is generated, from visible blue light to ASML’s exclusive extreme ultraviolet (EUV) technology.
Mercury lamps: from blue to UV
When ASML was founded, the state-of-the-art light source for lithography was the mercury vapor lamp. This generates light by passing electricity through a bulb that contains mercury. The current heats the mercury until it becomes a plasma that emits light of various wavelengths. The required wavelength was selected with an interference filter.
Our first lithography systems used this setup to create blue light with a wavelength of 436 nanometers (nm), known as the mercury g-line. They could print features as small as 1 micron (1,000 nm). To enable smaller features, we soon switched to invisible ultraviolet (UV) light with a wavelength of 365 nm. These later i-line systems pushed feature sizes below 1 micron, eventually reaching 220 nm.
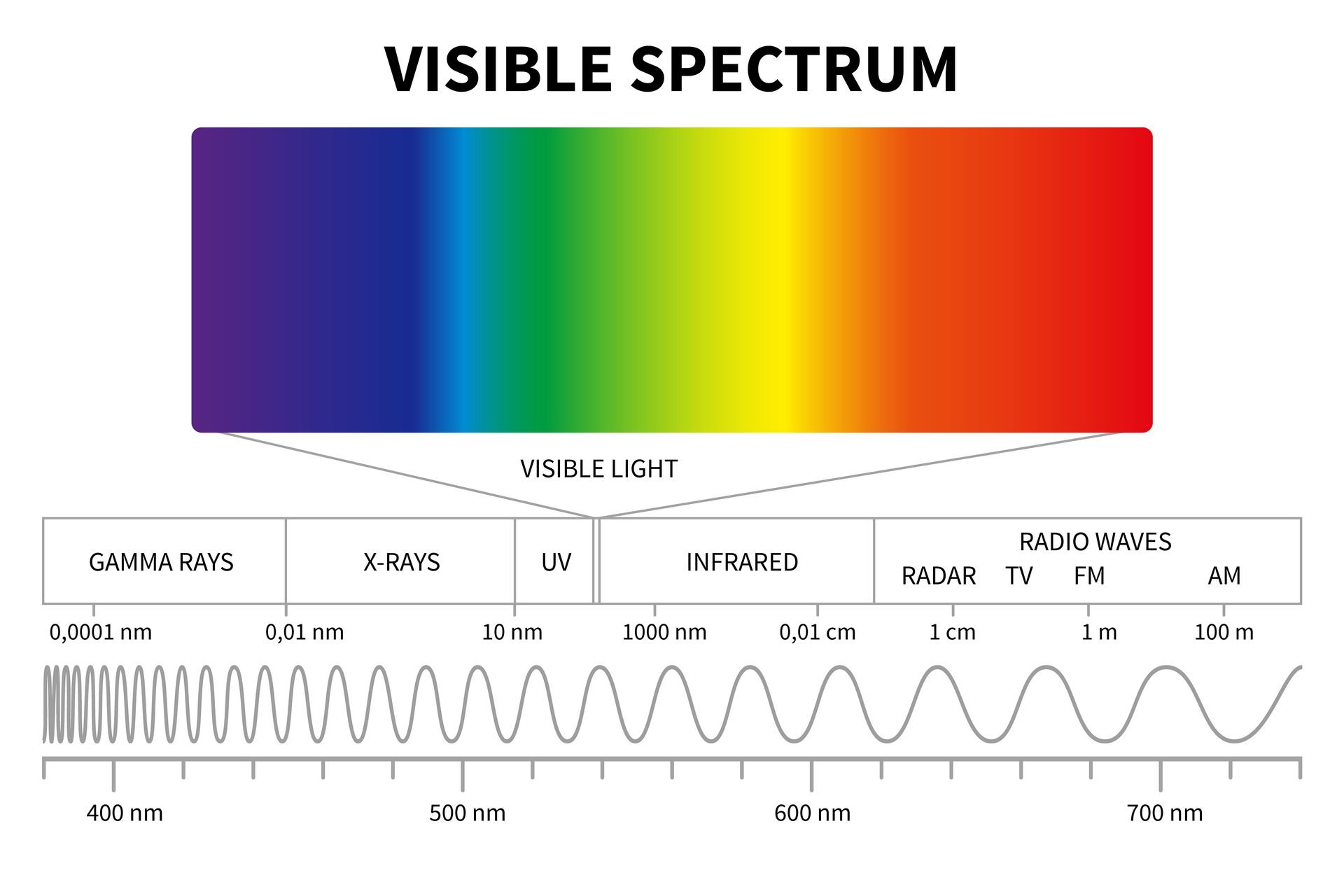
Lasers and DUV
In the mid-1980s, the industry demand for smaller features led to another shift to shorter wavelengths. And this time, a whole new way of making light was needed: lasers. In particular, deep ultraviolet (DUV) excimer lasers. These lasers use mixtures of gases that don’t normally combine. However, when enough energy is applied, atoms of the two gases join together to form excited temporary molecules (excimers). The excited molecules release excess energy as light whose wavelength depends on the gases used.
KrF: the DUV dawn
The first DUV systems used excimer lasers based on a combination of two elements: krypton and fluorine. These krypton-fluoride (KrF) lasers produce light with a wavelength of 248 nanometers (nm). 150 nm KrF systems shrank feature sizes from the 280 nm that was possible with previous i-line systems. Modern KrF systems can now produce features down to 80 nm.
Going deeper with ArF
Going even further into the UV spectrum, the next generation of DUV lithography systems use argon-fluoride (ArF) excimer lasers that produce light with a wavelength of 193 nm. This enabled features sizes of 38 nm to be printed.
Creating EUV light
EUV lithography, a technology entirely unique to ASML, uses light with a wavelength of 13.5 nanometers. This wavelength is more than 14 times shorter than DUV light.
EUV light occurs naturally in outer space. But to make EUV lithography possible, we needed to engineer a way to create such light within a system. So, we developed a radically new approach to generating light for lithography.
In our laser-produced plasma (LPP) source, molten tin droplets of around 25 microns in diameter are ejected from a generator at 70 meters per second. As they fall, the droplets are hit first by a low-intensity laser pulse that flattens them into a pancake shape. Then a more powerful laser pulse vaporizes the flattened droplet to create a plasma that emits EUV light. To produce enough light to manufacture microchips, this process is repeated 50,000 times every second.
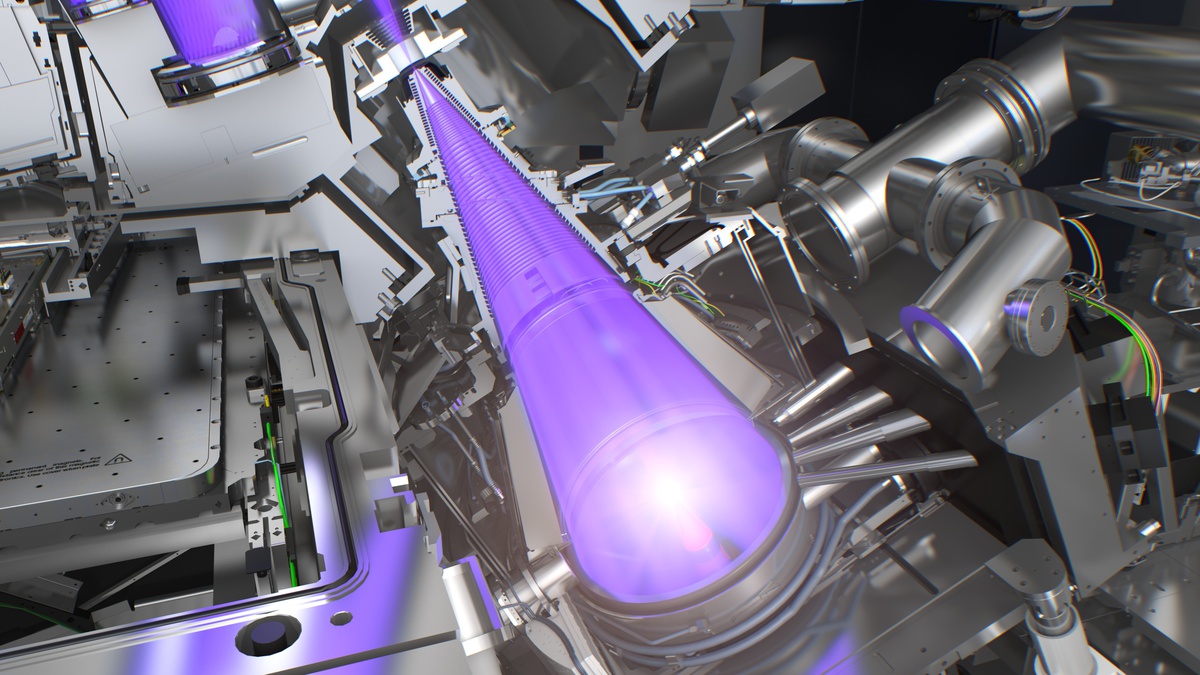
lithography principles
The science behind the chipMore about ASML technology
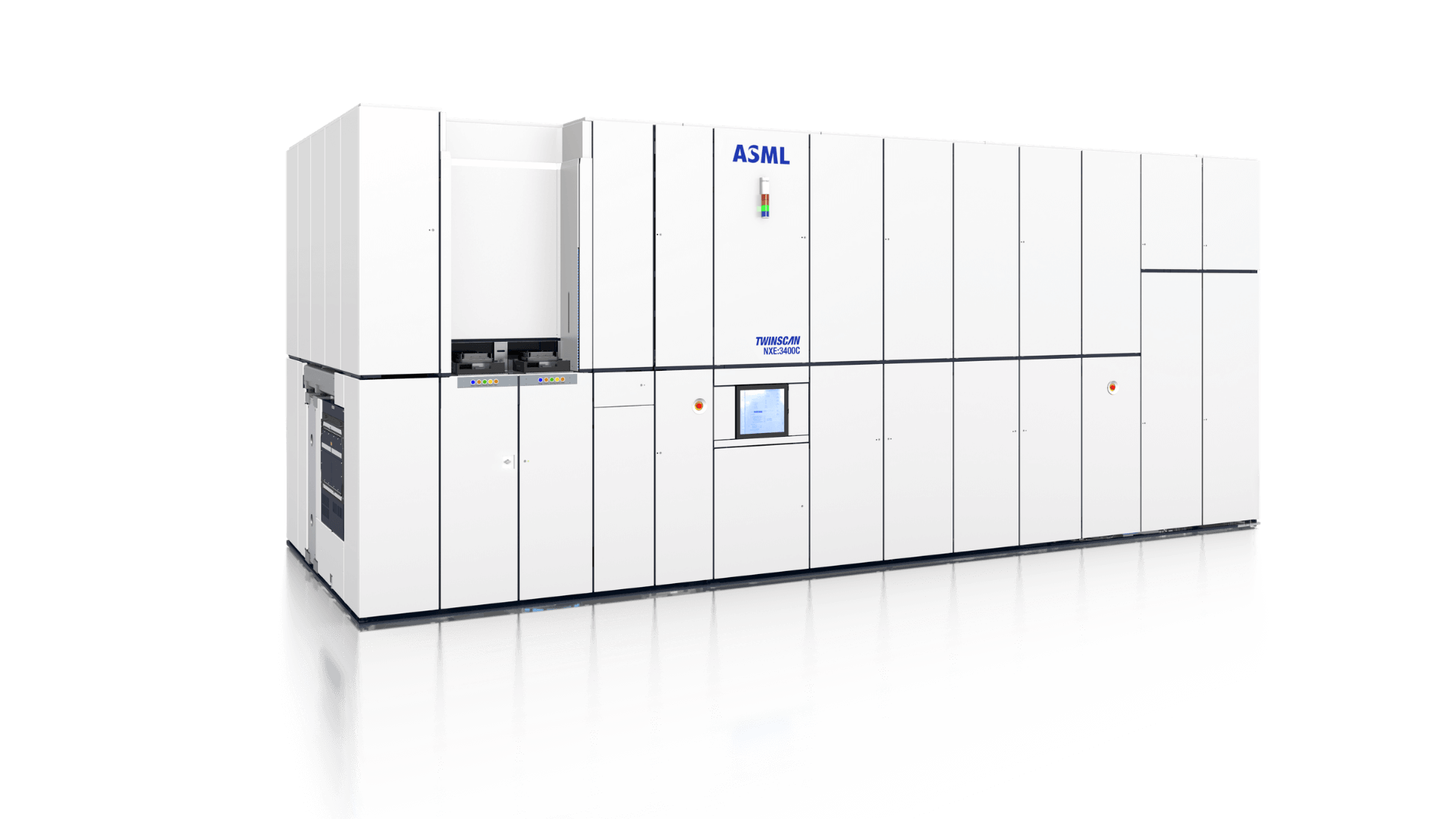
Providing highest resolution in high-volume manufacturing, ASML’s extreme ultraviolet lithography machines are pushing Moore’s Law forward.
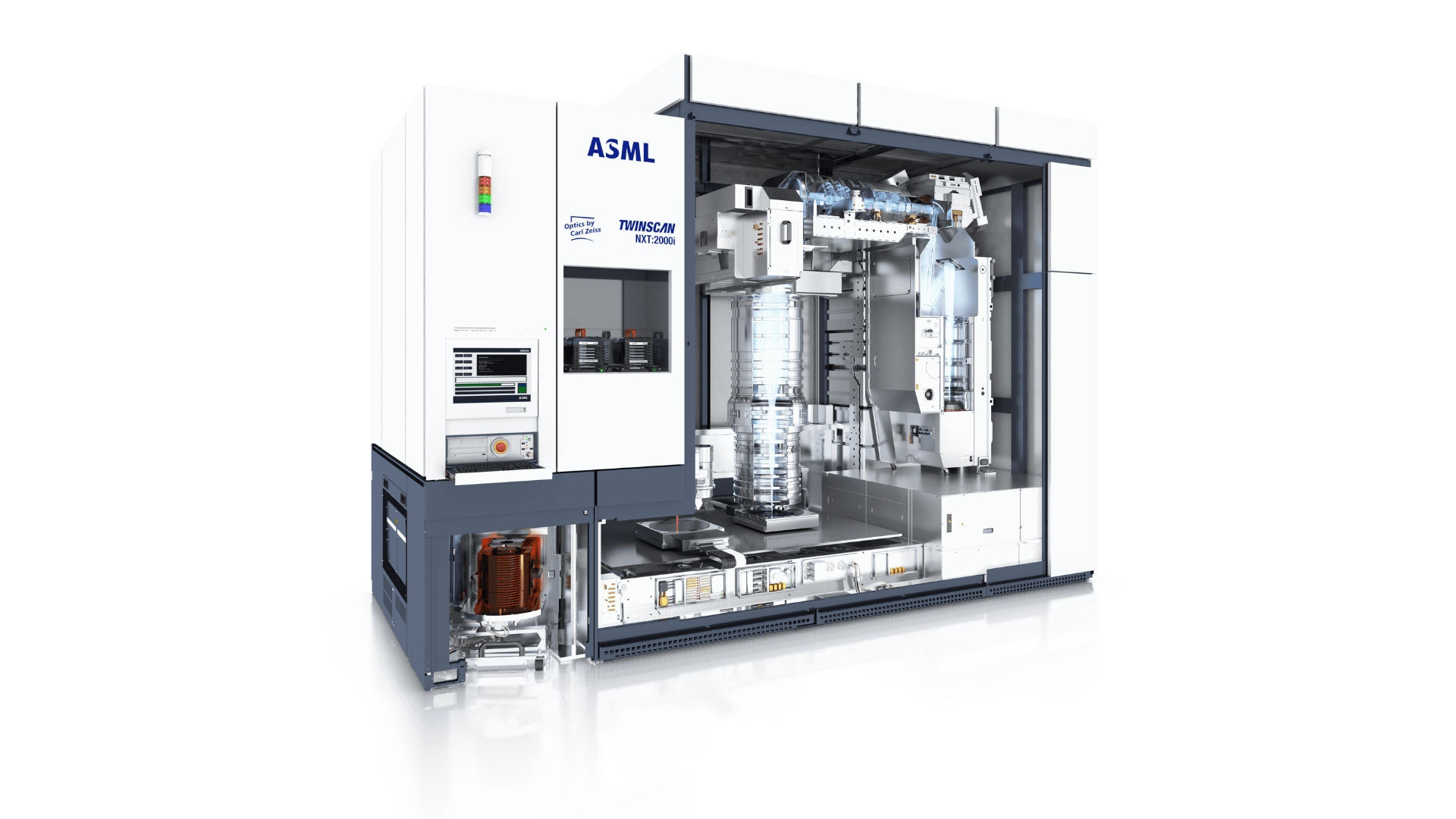
ASML's deep ultraviolet (DUV) lithography systems dive deep into the UV spectrum to print the tiny features that form the basis of the microchip.
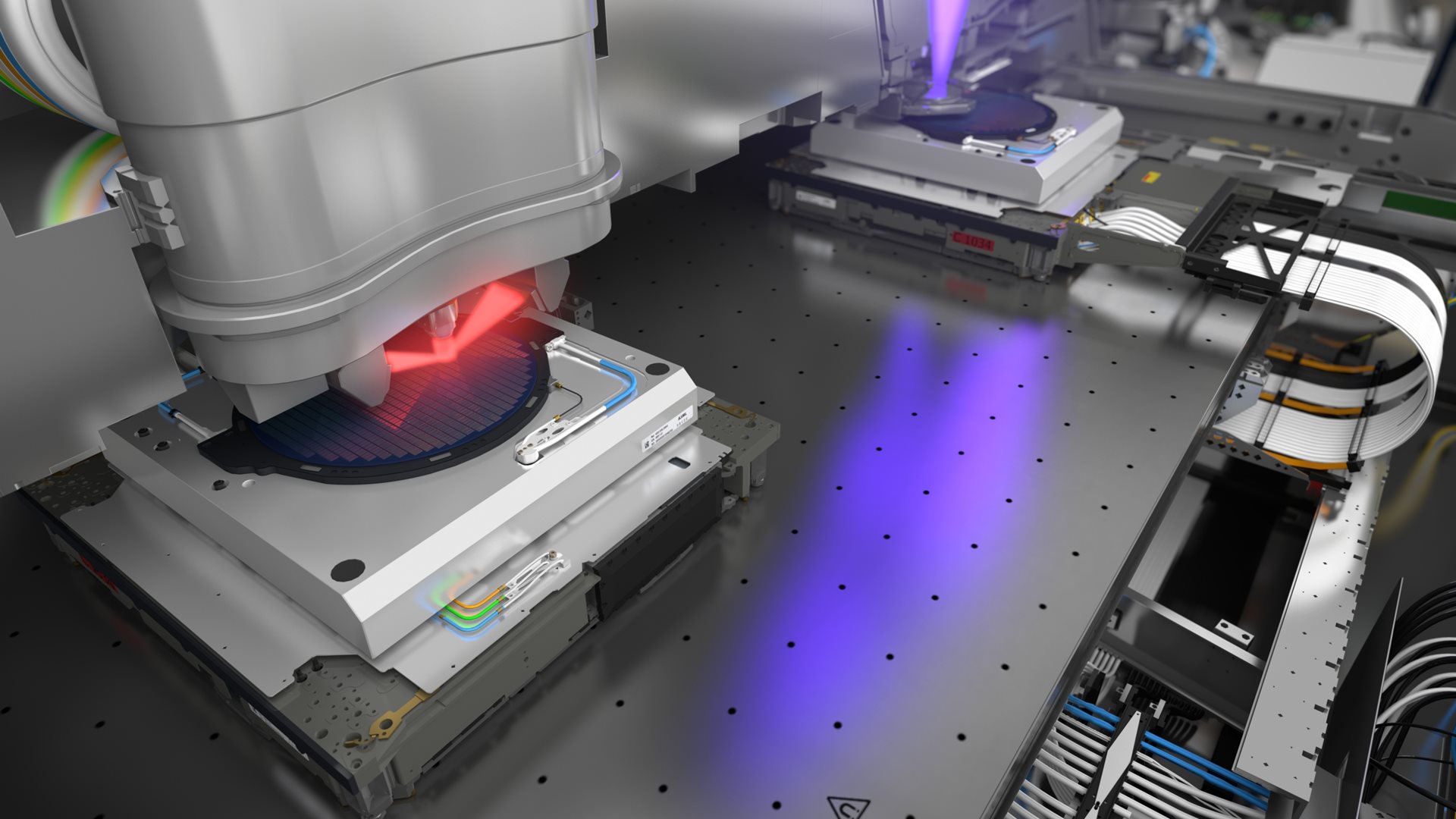
Delivering speed and accuracy, our metrology and inspection portfolio covers every step manufacturing processes, from R&D to mass production.
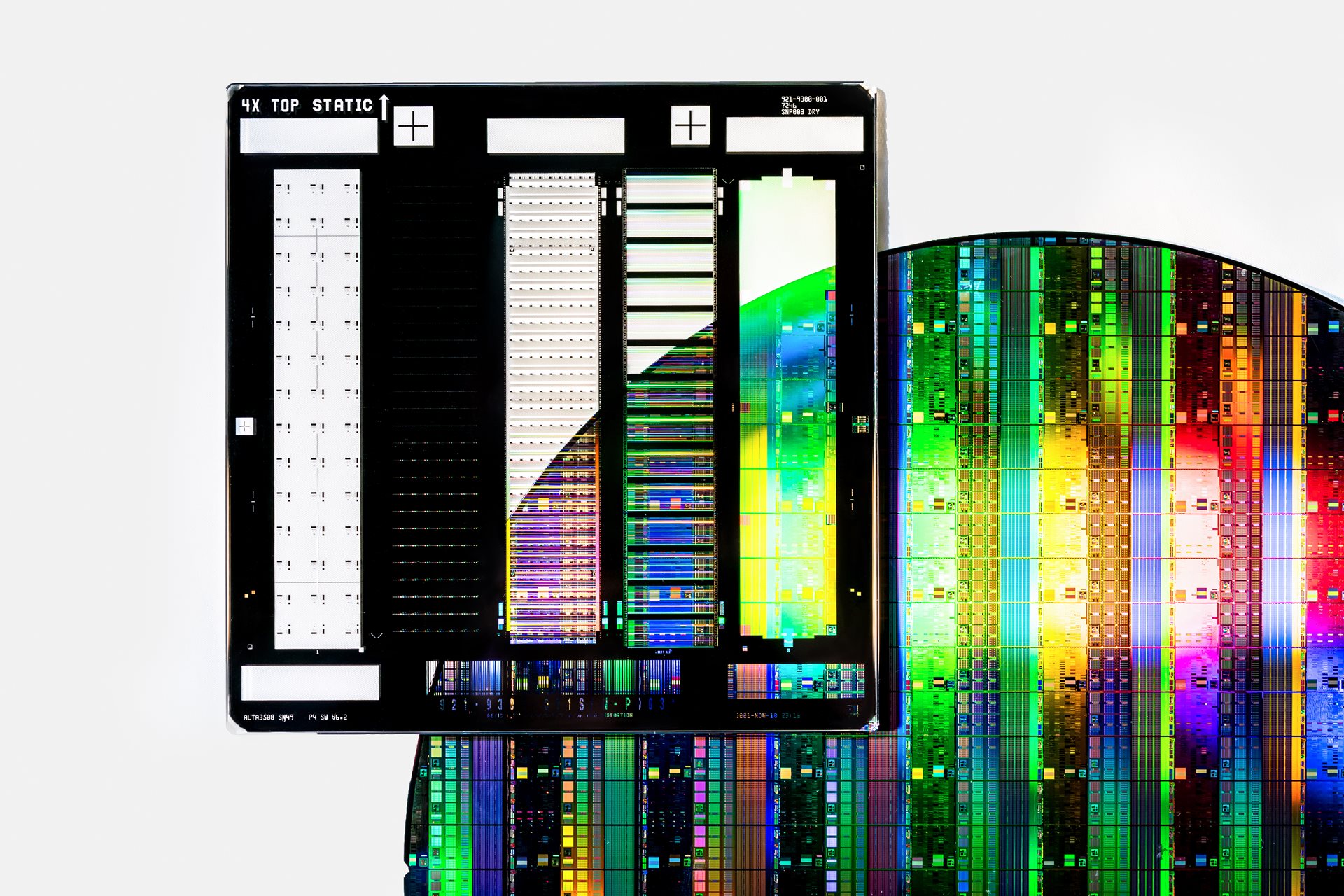
ASML's industry-leading computational lithography products enable accurate lithography simulations that help to improve chip yield and quality.