8-minute read - by Jessica Timings, July 22, 2021
Microchips. At almost every moment of every day, you’ll make use of technology that contains one of these small but mighty devices. Whether you are video chatting with a friend or waiting as a healthcare worker retrieves your COVID-19 vaccine from the fridge, there are chips at work all around you. Not to mention the cloud, data processing centers, the internet – all possible thanks to semiconductors. And yet – unless you work in tech – it’s unlikely you’ll spend much time thinking about the importance of chips to your daily life. That is, until they start to run short.
The global pandemic, digital transformation and the increasing demand for new technology has drawn all eyes to the semiconductor industry and the technology companies that make the digital world go round.
Why is there a global chip shortage?
The chip shortage is not so much about what went wrong, but what went right. Since the introduction of the smartphone, the internet has become accessible to almost everyone around the globe. Moving the vast amount of what we do online has led to an explosion in demand for fast, stable internet, while technological developments such as 5G, high-performance computing, artificial intelligence (AI) and the internet of things have accelerated digitalization and the demand for chips.
Then, in late 2019 came COVID-19. In early March 2020, many industries prepared to pull back in response to what was expected to be a significant blow to global and national economies. Many automotive and electronics companies decided to pause orders, including of semiconductors.
But COVID-19 had yet another important role to play in the shortage: user demand. As the world ground to a halt and nationwide lockdowns called for people to stay at home, online ordering ramped up. People purchased computers for home offices, fitness electronics to help stay healthy and gaming devices to entertain the kids. Digital devices became our primary method of connection with the outside world, allowing us to stay in touch with our colleagues, loved ones and monitor the progress of the pandemic. All this put immense pressure on the cloud, with tech companies needing to add capacity to their cloud centers, which in turn had a significant impact on the demand for microchips.
The pandemic hit the gas pedal on the accelerated pace of digitalization. Once industries realized that demand for their products had just temporarily stalled and was now actually accelerating, they needed to reverse their original planning. They prepared to go full steam ahead on new orders. But there was one tiny problem: semiconductors.
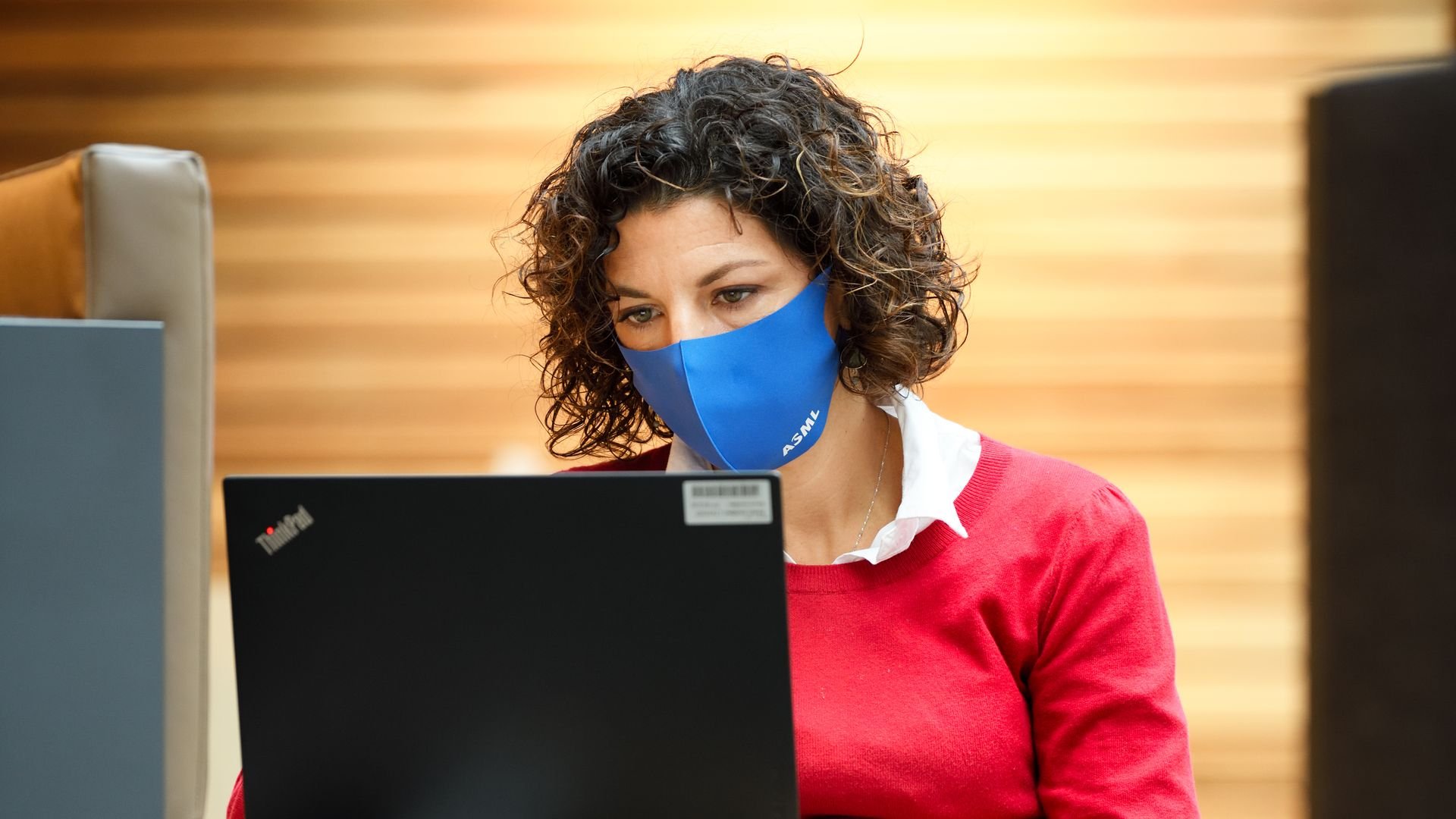
What’s so special about semiconductors?
Microchips are a unique product. Where nuts and bolts can be produced relatively simply, fabricating the layers on even the simplest microchip requires an elaborate process that few companies in the world have mastered.
During this process, which can take months from start to finished product, the silicon wafer will travel through dozens of different machines in a chipmaker’s fab (semiconductor fabrication plant), such as chemical processing equipment, inspection tools and lithography systems. Multiply that by the dozens of layers that together make up a chip – and this wafer has gone through over 3,000 steps before it leaves the semiconductor fab (which itself is a tightly controlled environment some 10,000 times cleaner than the outside air) and finds its way into electronic products.
The pandemic hit the gas pedal on the accelerated pace of digitalization.
This multifaceted production process has led, over decades, to the semiconductor industry becoming a global ecosystem. This ecosystem includes specialized chip design houses, equipment and infrastructure suppliers, as well as chipmakers themselves, who both collaborate and are in fierce competition at the same time. So, when companies halted chip orders due to COVID-19, these decisions caused a ripple effect down the semiconductor supply chain: our customers, the chipmakers, were cautious about the impact of these changes in demand, so they adjusted their orders from suppliers. In turn, ASML also adjusted commitments in its supply chain.
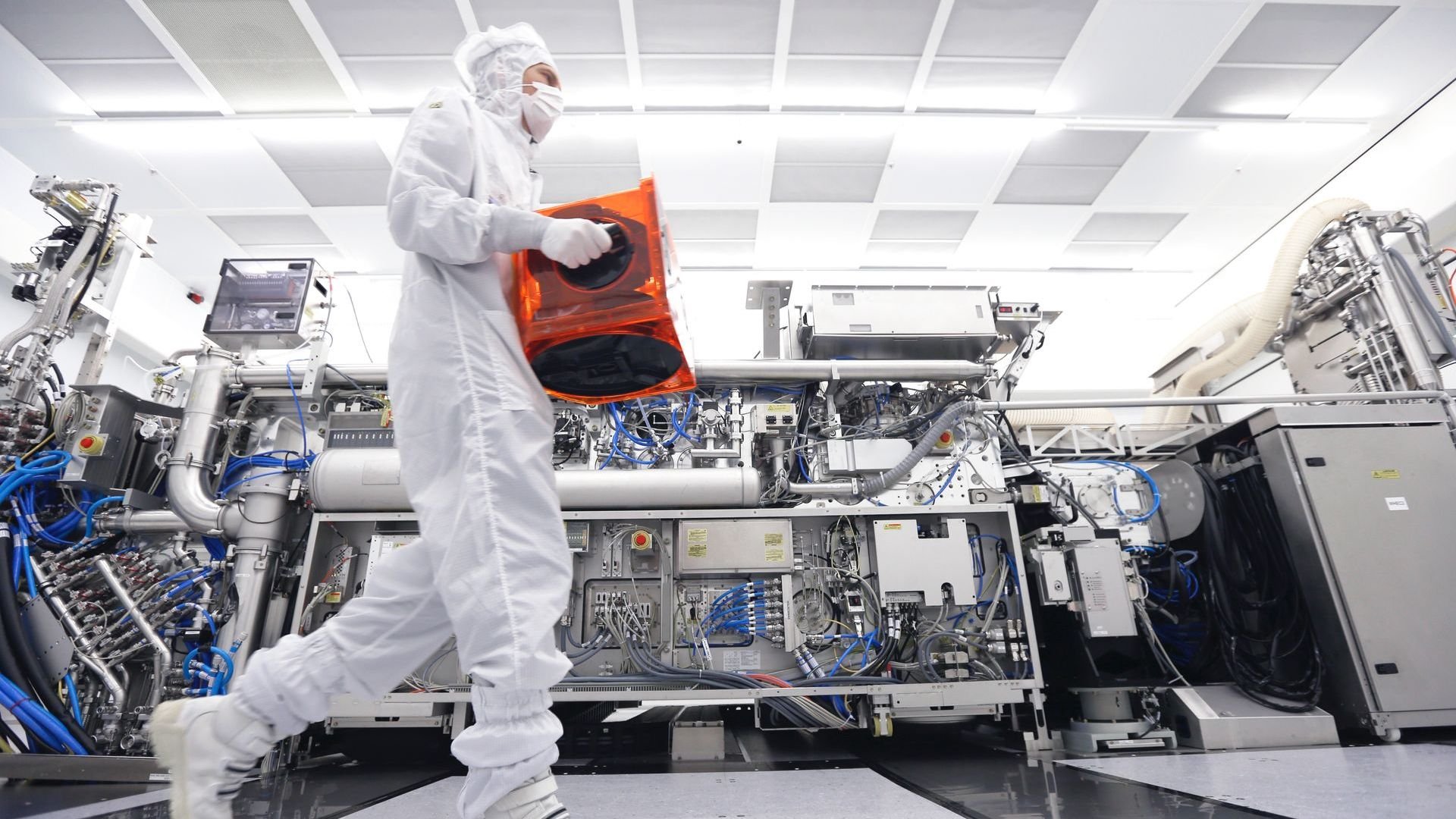
So where does ASML fit in the semiconductor shortage?
ASML’s lithography systems use light to fabricate the circuitry patterns on silicon wafers, a critical step in the chip manufacturing process. The patterns link together as a single integrated circuit that can offer computing or memory function. Lithography systems can be found in the factories of every major chipmaking company in the world.
Over decades, companies across different technical sectors and countries have worked together as part of the global semiconductor ecosystem.
But our systems are just one piece of a process involving numerous suppliers and chip equipment. Every step and every machine in the process is important. For example, layers that have been printed on a wafer by means of lithography must also be etched, where excess material is removed through a chemical process to reveal the patterns that create the 3D circuit. Then a new layer is added and the process starts all over again. That is why all production stages and various tools must be aligned perfectly to ensure the highest possible manufacturing yield.
This interdependency is another reason the semiconductor industry is unique. Over decades, companies across different technical sectors and countries have worked together as part of the global semiconductor ecosystem. From academics who help us understand and bend the laws of physics to customers who identify new possibilities and suppliers that translate our ideas into products and technology – we collaborate to succeed. And now, together, we are gearing up to meet the chip demand.
What is ASML doing about the chip shortage?
Addressing a global chip shortage in the middle of a pandemic is no easy feat, but those who work at ASML love a challenge. Shipping new systems, supporting fast installs and improving the availability and efficiency of installed systems, including through upgrades, are key ways we are helping our customers get on top of this shortage.
Ramping up productivity
Chipmakers wanted to increase their wafer output, and boosting lithography as the critical manufacturing step was clearly one way to do that. To help ramp up productivity, we first looked to productivity upgrades in the installed base. These upgrades, which we refer to as a 'productivity enhancement package', can be installed quickly and are the most effective and efficient way to increase the productivity so that a system can produce more wafers per hour. Typically, productivity upgrades include software upgrades and hardware innovations.
Hardware, such as an upgraded vessel for the light source and different illumination settings to increase wafer yield, can also increase productivity. However, this requires system downtime. And in a time where you can’t make enough wafers, this is not ideal. To manage this, we’re working with our customers to optimize the timing of their upgrades and future-proof their production lines.
Manufacturing and allocating systems
Responding to this shortage requires a holistic response across ASML’s entire product portfolio, which spans DUV, EUV, metrology and inspection systems, software and services.
We know that our systems are critical in meeting this surge in demand, particularly in delivering some of the more advanced chips, where our EUV systems play an important role in affordable manufacturing. We are planning to increase our system output. For EUV, we have already begun shipping NXE:3600D systems that have a 15–20% higher productivity than their predecessor, the NXE:3400C. As well as shipping systems that increase productivity, we're regularly aligning with our customers to support their technology needs and reach their required wafer capacity.
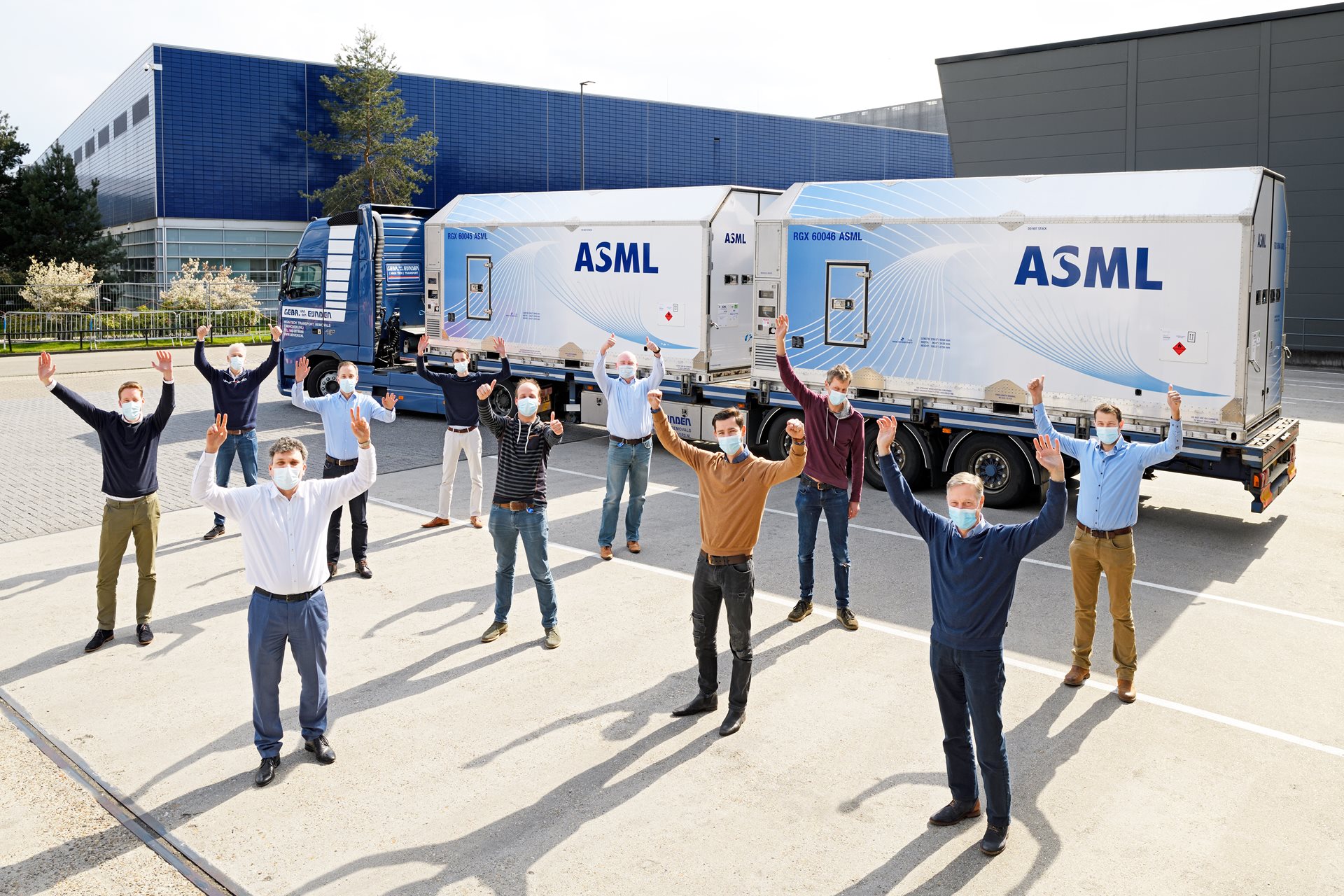
While you may think that simply purchasing more chip equipment might solve the chip shortage, buying an ASML system couldn’t be more different to shopping for appliances online and getting it the next day. It simply takes a while for a lithography system to be built. The thousands of components that comprise – for example – an EUV system are made up of more than 100,000 individual parts, which must be manufactured with great care and delivered from around the world: mirrors with layers polished to an atom’s thickness that take months to make are manufactured in Germany and the vessel for lasers that generate light by blasting tin droplets are developed in San Diego, for example. Once these many parts have been assembled and the system has been tested and approved, it is taken apart again in big chunks, and three airplane carriers transport the machine to the customer’s factory. You’ll also need a cleanroom roughly the size of a swimming pool just to house this machine.
As well as shipping systems that increase productivity, we're regularly aligning with our customers to support their technology needs and reach their required wafer capacity.
In order to support the strong demand in DUV lithography, the workhorse of the industry, we are also piloting a program to shorten the production cycle time for our DUV TWINSCAN NXT:1980Di and NXT:2000i products. Through this program, we’re aiming to free up a cleanroom cabin earlier so the assembly of a new system can start by allowing for some assembly, qualification and calibration to occur on the customer site, while balancing risks to ensure that we are delivering high quality. In early 2021, the first system through this program was successfully installed at a customer fab.
When will the microchip shortage end?
It will not be easy to solve the shortage of chips that we are seeing today. Peter Wennink, our CEO, recently explained his outlook: “2020 – the COVID year – was really a year where customers were cautious. Looking back, too cautious. So that underspend you could call is now translating into demand for 2021. Of course that will take some time before we have our output ramped up.” In his view, catching up with the demand on output could take up until 2022.
Pat Gelsinger, Intel’s CEO, says the move online during the COVID-19 pandemic has led to a "cycle of explosive growth in semiconductors.” He adds that, “while the industry has taken steps to address near term constraints, it could still take a couple of years for the ecosystem to address shortages of foundry capacity, substrates and components."
TSMC Chairman Mark Liu is optimistic about their ability to get up to speed. "Today, we think … that we can catch up the minimum requirement of our customers, before the end of June [2020].” But, as he puts it, this doesn’t mean the shortage will be solved so quickly. “There's a time lag. In car chips particularly, the supply chain is long and complex. The supply takes about seven to eight months," he adds.
It's clear that the demand for semiconductors will continue to grow, the huge collaborative network we call the semiconductor industry will increase its capacity and we will keep innovating to fuel the digital future. Peter describes it this way: "We strongly believe that this growth cannot be supported by the capacity that we currently have. So we need to extend our capacity by doing things faster through cycle time reduction, adding more people and more machines, and building square meters."
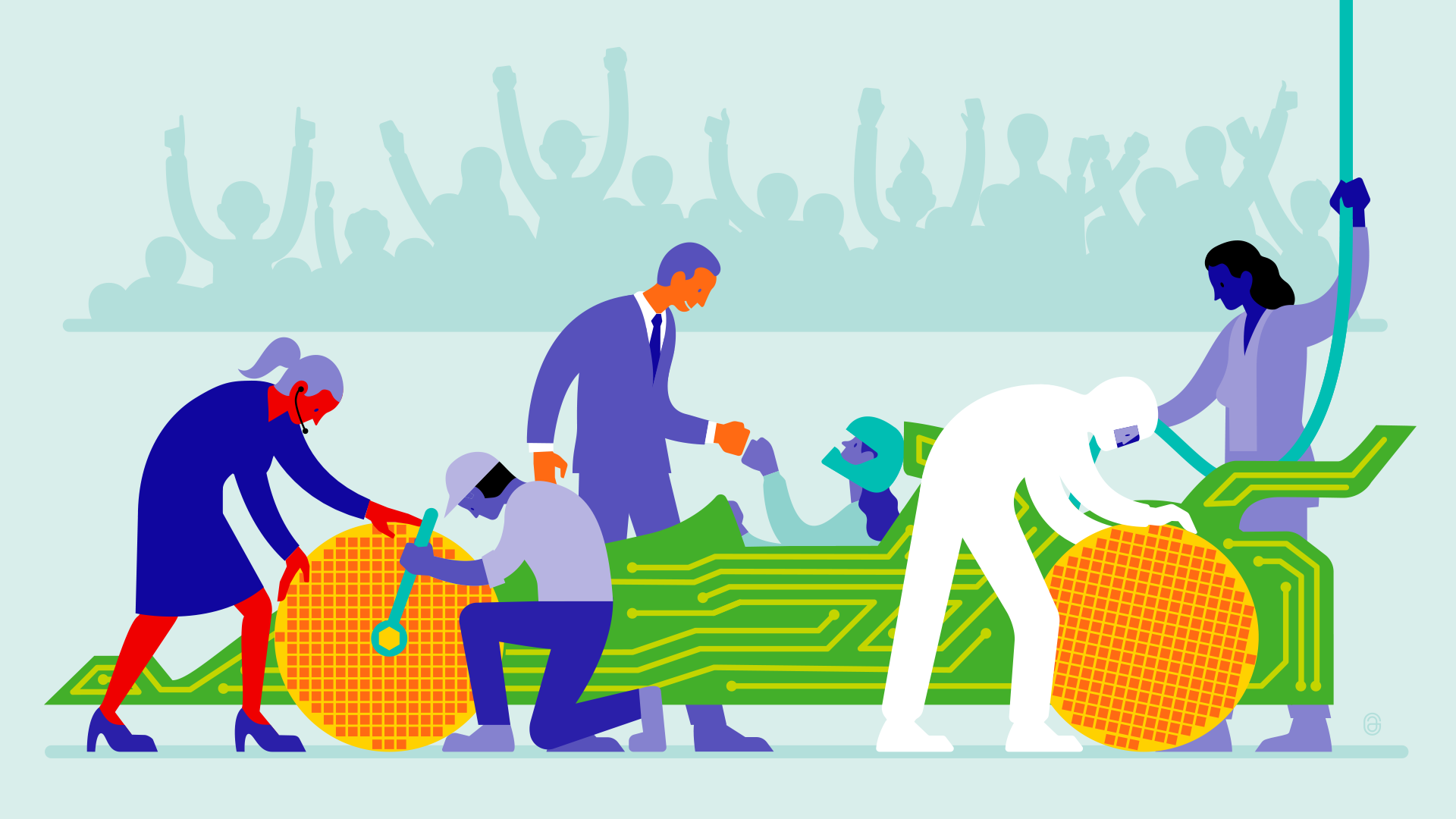