6-minute read - by Kate Brunton, May 25, 2022
As an engineer, wouldn’t you like to know that the company you’re working for is trying to make the world a better place? That the products you design or service won’t contribute to the environmental crisis, and are so well made that customers will still be using them decades from now? That’s exactly the kind of approach we’ve adopted toward our products at ASML.
Sustainability in the semiconductor industry
“The semiconductor industry has a problem,” the Guardian declared in a September 2021 article. Paradoxically, semiconductors are necessary in order to meet global climate goals, but the microchip manufacturing process has a big carbon footprint – it requires large amounts of energy and water and creates hazardous waste.
Companies in the semiconductor industry recognize their impact and are setting sustainability targets. Our long-standing customer Intel recently pledged to reach net zero emissions by 2040 (following TSMC’s similar announcement) and many more companies are following suit.
ASML is no exception. In his message to stakeholders in our 2021 annual report, ASML President & CEO Peter Wennink cited climate change as the reason ASML is increasing its focus on environmental, social and governance (ESG) sustainability. “Climate change is a global challenge that requires urgent action by everyone,” he said. ASML has expanded its efforts from five focus areas to a nine-part strategy aimed at contributing to the United Nations’ Sustainable Development Goals. “We’re doing this because we recognize ESG’s increasing importance to all our stakeholders, but first and foremost, because it’s simply the right thing to do.”
Reduce, re-use, recycle
When it comes to the environment, one of our two main focus areas is circular economy. Instead of the ‘take, make, use, dispose’ model of a linear economy, we aim to reduce waste in our operations by recycling and by repairing and re-using parts, tools and packaging. In addition to investing in the energy efficiency of our products to help reduce the energy needed to produce microchips, “We have a strong roadmap to reduce waste,” says ASML President & CTO Martin van den Brink, who has made it his personal mission within the company to eradicate waste – in products, resources and processes. Our targets for reducing waste include reducing the amount of waste generated in kg per € million revenue by 50% in 2025 compared to 2019 while at the same time increasing our material recycling to 85% by 2025 (for more information, download our 2021 annual report).
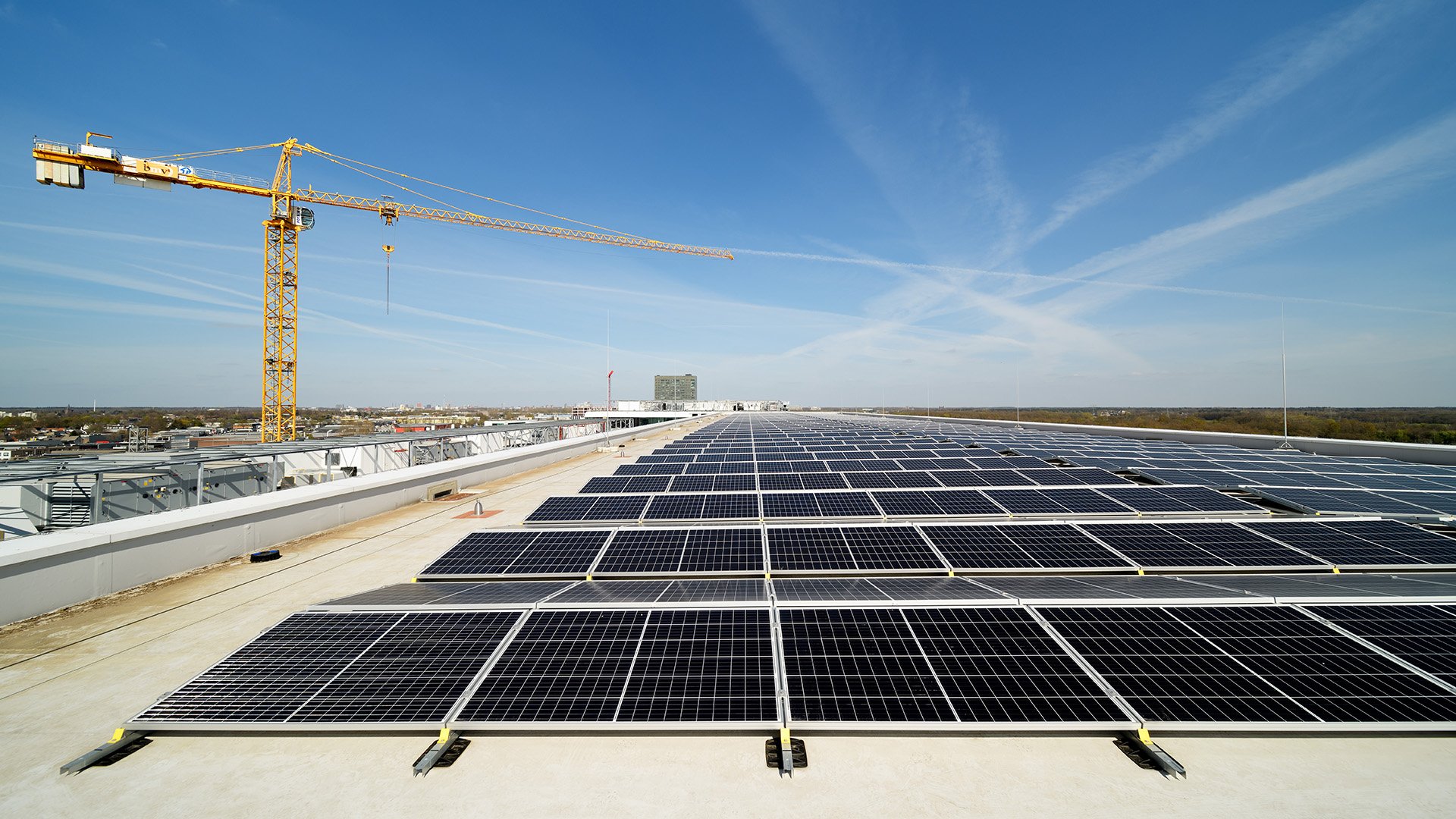
Designing for re-use
However, “It’s not enough to simply identify what we can currently recycle and re-use and call it a day,” says Jules Tops, head of Re-use at ASML. “We have to embed waste reduction into how we design our products.”
The cross-departmental Re-use team at ASML focuses on several design principles, including the repairability and upgradeability of parts (which involves creating design commonality among machines within and across product platforms).
“If we design a part that's not repairable, that's waste,” says Jules. “If we know that the part will have to be replaced in a customer fab, we need to make it repairable.” ASML remanufactures as many used machine parts as possible, qualifying to the same standard as new parts.
One example of how we’re designing for re-use is the tin catchment systems in our EUV lithography machines. The light source in these advanced systems works by firing a laser pulse at a tiny droplet of tin twice – first to flatten it, and then again to vaporize it, producing a plasma that emits extreme UV light. It repeats this process 50,000 times per second (yes, you read that right). The tin waste from the process is collected in ‘buckets’ that would normally be thrown away, but our R&D teams in Veldhoven, the Netherlands and San Diego, California worked with our supplier VDL to develop a way in which the tin can be extracted and repurposed and the buckets re-used.
“We also try to avoid ‘iterative design waste’,” Jules explains. “If we’re designing a new part or new version of a part, it’s typically cutting-edge technology, so it’s often trial and error, and it doesn’t always work. We help R&D teams to develop risk-mitigation strategies to minimize potential scrap, and to ‘learn fast’ to avoid repeats in parts failures.”
Optimizing sourcing & logistics processes
Another potential source of waste at ASML is surplus parts supply, so the Re-use team works closely with our Sourcing & Supply Chain team and logistics teams to make sure that back-up materials are only ordered when there’s a clear demand. According to ASML industrial engineer and re-use ‘ambassador’ Mirjam van Geel, “Less is more – preventing waste is better than re-use. That’s why we’re trying to ‘close the tap’ on materials that aren’t required.”
“Less is more – preventing waste is better than re-use. That’s why we’re trying to ‘close the tap’ on materials that aren’t required.”
The Logistics department is a valuable partner in reducing packaging waste. In 2021, we were able to re-use more than 4,300 metric tons of materials used to pack and transport parts between our factories and customer fabs. “We want to re-use packaging, but actually, we’re also striving to use less packaging in the first place,” says Jules. One way in which we’re accomplishing that is by building local parts repair and distribution centers close to our main customer sites. “This makes it easier for us to repair parts quickly and reduces the amount of packaging needed to transport the parts to and from the customer fabs,” he continues. This localization strategy also helps to reduce the amount of CO2 we produce during transportation, and it turned out to be instrumental in keeping our business running smoothly during the COVID-19 pandemic.
Changing our mindset
Sustainable quality that lasts a lifetime has always been at the center of our design approach. The modular design of our products enables us to upgrade our machines to higher performance levels directly at a customer site rather than having to replace the entire product. Almost 94% of the lithography systems we’ve ever sold are still in use at customer sites today, and we also dedicate a part of our business to refurbishing our classic PAS 5500 and TWINSCAN lithography machines for a new life and a new purpose.
But the challenge now, according to Jules, is reprogramming our brains to accommodate a new definition of ‘quality’. “Quality products that leave a trail of waste behind them are not truly quality products,” he says.
“Quality products that leave a trail of waste behind them are not truly quality products.”
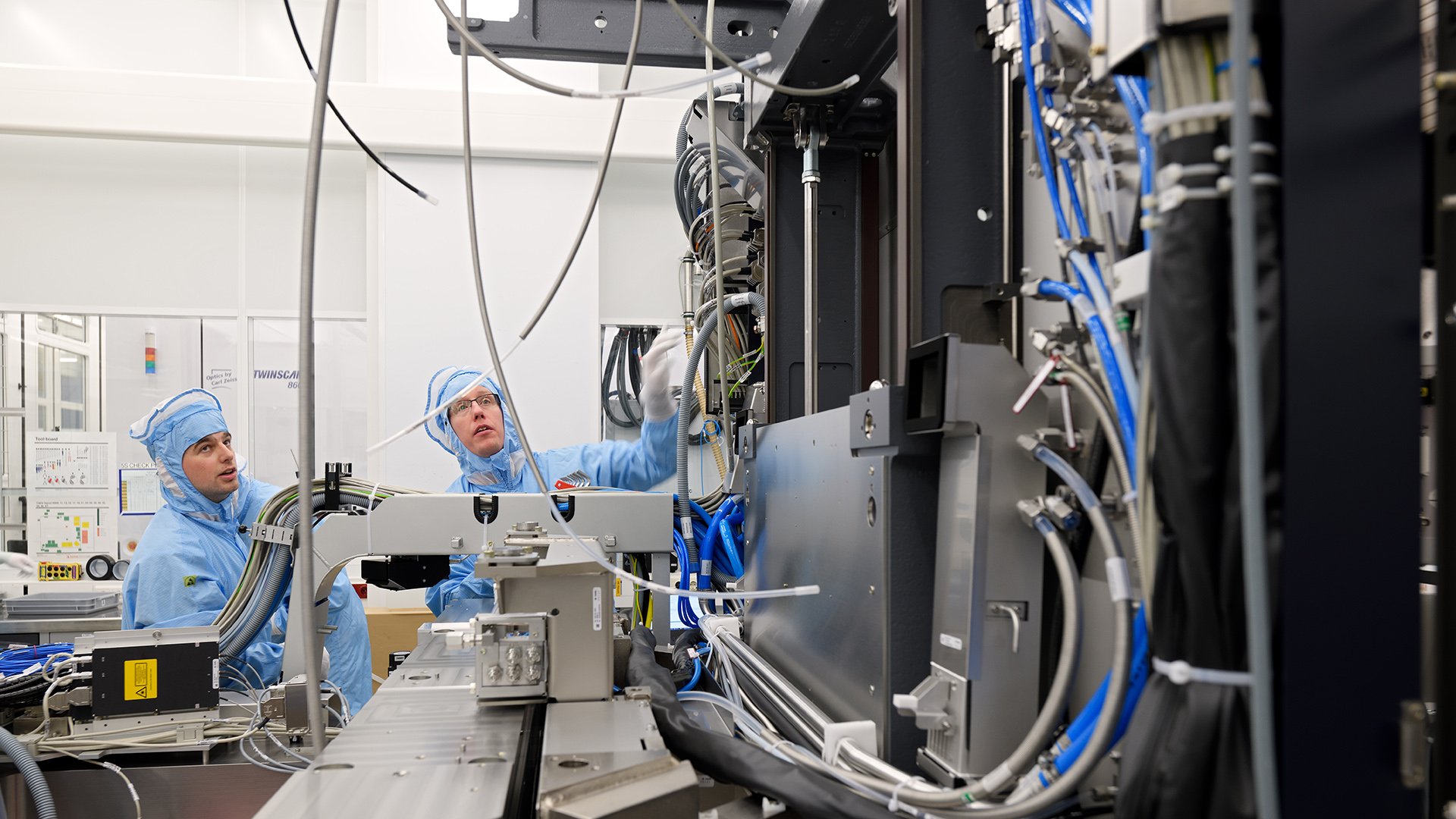
An example of this mindset shift involved updating our cosmetic guidelines to take re-use into account. “Previously, our guidelines would hardly allow any scratches on a part, but it’s natural to get some wear and tear on a part when it’s being used in the field,” Jules explains. “We had to change our guidelines and educate our R&D engineers and our teams at customer sites that ‘as good as new’ can mean having a few scratches here and there. So long as the functionality isn’t affected, our customers appreciate these parts like new ones.”
Helping the environment helps everyone
“Reducing waste is the right thing to do for the environment, but it also helps our customers, and helps us to reduce costs as well,” says Jules. “Customers are very eager to collaborate with us on re-use. Intel was actually the first customer to adopt our remanufactured parts program because it aligns with their sustainability objectives, and last year, SK hynix gave our local repair team an award for social responsibility.”
Keeping repairs local is key, explains Customer Support re-use program manager Seung-Yong Jin. “The more we can re-use at centers located near customer fabs, the better we can ensure that the materials are available when and where our customers need them.”
Linking the chain together
ASML also encourages its suppliers to take part in efforts toward circularity. In fact, it’s one of the seven core building blocks of our supplier sustainability program. “Our suppliers design parts that we then use in our machines, so we need to involve them in our re-use process,” says Jules. “Up front, you can never tell what kind of logistics development challenges you’re going to run into, so we really have to learn together with our suppliers.”
CTO Martin van den Brink recently went on a tour of our supplier Prodrive Technologies near our headquarters in the Brainport Eindhoven region. During the visit, the two companies agreed on several guidelines for repairing parts in an effort to promote re-use. “We even agreed that they would send us case examples of the parts that they aren’t able to repair, to see if we can alter the design or find some other way to improve re-usability,” says Jules.
The demand for ASML machines is soaring amid global chip shortages. In this story on the history of EUV technology, vice president of our EUV Factory Sheila Leenders acknowledges that in ramping up our production of EUV machines, “Our supply base is facing the challenge of a lifetime.” Jules is convinced that re-use and circularity will play a major role in meeting the demands of our customers. “If ASML and our suppliers can repair and re-use as many parts as possible, we take some of the burden away from our supply chain and allow them to focus on delivering the new parts needed for our machines,” he says.
“Our supply base is facing the challenge of a lifetime.”
“My hope is that we can make re-use the path of least resistance – so familiar and easy that throwing something away actually costs you effort,” Jules concludes. “Circularity is not something you can choose to prioritize or not – at ASML, it's part of delivering quality products we can be proud of.”
Want to join us as an engineer at ASML? Check out our latest R&D jobs.